Ceramic Artist Beverly Marusa shares ceramic and pottery making tips, marketing fine craft links and information, ceramic artist links, ceramic reference materials, and much more with a focus on the emerging ceramic artist.
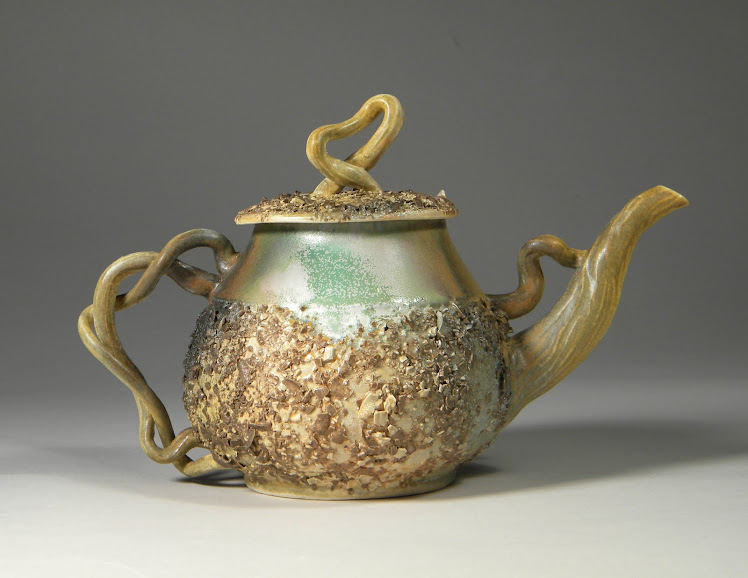
Thursday, April 14, 2011
Thank you Claystation
Thank you Claystation for listing Marusa Ceramics and Pottery Blog as one of the top 30 ceramic blogs! I am flattered and grateful!
Another Great Article from Ceramic Arts Daily
I've mentioned in the past that it can be very challenging to achieve glaze interest when firing to cone 6 in oxidation. Ceramics Arts Daily's featured article today was by glaze expert John Britt. John was generous enough to share some of his hare's fur and oil spot glazes in the article and the pictures are absolutely stunning. He achieves the beauty of his cone 6 recipes by layering two glazes.
Layering glazes is often employed by ceramic artists who fire in this range and atmosphere and it's great to try different glazes in the process. Of course some combinations work and others don't so always use test tiles or larger pieces that didn't fair well in the bisque firing to experiment with new glaze combinations. I like using the larger pieces to get a good feel for how the glazes will react on different textures and will often throw small cups or bowls for this purpose. Anyway, here is the link for John Britt's article on Ceramic Arts Daily
Wednesday, March 2, 2011
An Insightful Film Addressing the Challenges of Female Artists
Here's a link to the trailer and website for a film that I hope to see in the near future: "Who Does She Think She Is"
Tuesday, February 22, 2011
Experimenting with Different Styles
I really enjoyed reading today's featured article from Ceramic Arts Daily. It is an interview with an established artist who seems to have abruptly changed his style. Here's the link: Ceramic Arts Daily's Interview with Nick Joerling
I agree that it's important to keep experimenting in the studio. One's medium should be considered one's voice or possibly one's "vocabulary" as one of my former professors, Dave Williamson, would say. It always helps to consider a message or viewpoint to convey in your work and then ask yourself how you could communicate that using your "vocabulary."
Another thing to consider when designing new work is a quote that I read several years ago made by a ceramics professor who would challenge her students by telling them "Show me a pot that I've never seen before." Unfortunately, I can not remember that professor's name. If anyone else is familiar with the quote, please let me know the name of the author so that I may give them proper credit.
Wednesday, January 26, 2011
Cone 6 Wine Red Glaze
I promised glaze recipes earlier in this blog so here is my new favorite glaze. The recipe was first printed in Clay Times in the March/April 2005 edition by Richard Burkett. His recipe included the addition of .25 cobalt carbonate but without it, it's a beautiful wine red breaking white where thin. Thinner coats of glaze produce a mottled wine and white surface. Thicker coats produce a more solid colored wine. The glaze has not run for me and has a nice semi-gloss appearance. Slow cooling has little effect on this glaze but will change the color slightly to more of a burgundy than red. My test firing was done in oxidation and I do not know what the results would be in reduction.
32 Silica (flint)
21 Gerstley Borate
20 Calcium Carbonite (whiting)
16 Nepheline Syenite
11 EPK (kaolin)
5 Tin Dioxide
.15 Chrome Oxide (chromium green)
Tuesday, January 11, 2011
Achieving Opacity in Glazes
I made my trip to stock up on raw materials and clay yesterday and was floored by the increased price of tin! It was more than double the cost of what I paid last year. Tin is used as an opacifier in glazes and also to achieve reds and pinks in midfire glazes. Due to cost, I've decided to save my tin for chrome-red glazes and substitute other opacifiers in various glazes. I've spent the morning researching my alternatives online and in Robin Hopper's book "The Ceramic Spectrum." The following link to the site Digital Fire had a pretty good list of opacifiers and covered most of what was in Robin Hopper's book. However, Hopper also mentions that Clays and Feldspars may act as opacifiers as well. These work similar to one another as a glaze will only absorb so much clay before the remainder remains unmelted. The glazes made in this manner would have an opaque matte character and may have a dry underfired look. I prefer matte glazes achieved by the formation of small crystals formed by slow cooling. Some of the materials that aid in the process are: lithium, barium (I prefer not to use this for toxicity reasons), zinc, potassium, magnesium, sodium, and iron.
Tuesday, January 4, 2011
Glaze Simulator Website
Here's another awesome link to a free glaze simulator website. It enables you to enter your glaze ingredients when developing glazes and it will analyze those recipes for you: http://www.glazesimulator.com/
I also strongly recommend the following site if you fire to midrange cone 6: Electric Midrange Cone 6 Potters http://cone6pots.ning.com/ The following discussion is truly worthwhile no matter to what range you fire: "How to direct your pottery knowledge to a business"
Bill Van Gilder Cone 6 Glaze Recipes
Happy New Year Everyone! I apologize for not posting for awhile but it has been a busy holiday season. Here's a link to some glaze recipes that Bill Van Gilder has generously shared. I am firing a test tile of his Crocus Martis Red today. I used red iron oxide in place of crocus martis. I'll let you know how it goes. I have been searching for a good cone 6 red glaze and would be very appreciative if anyone has a good recipe and would like to share.
http://www.vangilderpottery.com/glaze/vangilder%20CONE%206%20OXIDATION.pdfUPDATE:
Well, it turned out to be a beautiful brown glaze with small reddish crystals. I've tried firing to cone 6 and then slow cooling to 1650 degrees Fahrenheit and holding for 30 minutes. I also tried re-firing to 1650 and holding for one hour. The glaze coloring remained the same for both tests. However, the slow cooled firing produced a semi gloss glaze and the re-fire produced a matte appearance. It does look beautiful with the wine red glaze though so it's definitely a keeper. I intend to pick up a Spanish red iron oxide or crocus martis at a later date and use that in place of the red iron oxide to see if it makes a difference.
Subscribe to:
Posts (Atom)